The Science of Rubber
The science of rubber
Rubbers are made up of long hydrocarbon polymer chains. Polymers are long chains made up of many repeating smaller units which are called monomers. A single polymer molecule can be thousands of atoms long.
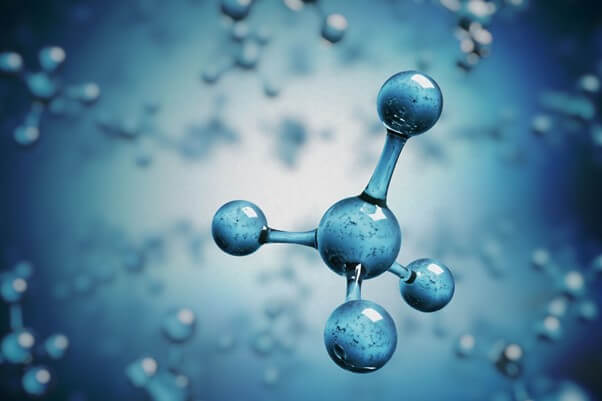
How do monomers become polymers?
Polymers are formed in a process called polymerisation in which the monomers are joined together either by addition polymerisation or condensation polymerisation.
What is polymerisation?
Polymerisation occurs when the conditions are met for monomers to join together and form chains. The perfect environment involves the monomers being subjected to either pressure, changes in temperature or a catalyst. Should these conditions be met monomers will combine to form polymers.
What is condensation polymerisation?
Condensation polymerisation is a reaction that produces water as a by-product. This type of polymerisation occurs when the monomers contain a hydroxyl group. A hydroxyl group is an oxygen and hydrogen atom bonded together. Most rubbers are formed by addition polymerisation.
What is addition polymerisation?
This process simply involves the “addition” of single monomers to each other without creating any by-products. Addition polymers are formed when double bonds within the monomers are broken. One bond within the double bond is broken causing the double bond to “open up”.
This open bond allows the monomer to join to another monomer which has also “opened up”. This process can continue until an infinitely long chain is formed. The number of repeating monomer units in the polymer is known as the degree of polymerisation. As the degree of polymerisation increases, the density of the material increases as well as the melting and boiling points.
What are copolymers and terpolymers?
Both the length of the polymer chain and the type of monomer in the chain can affect the properties of the final material. Polymers can be made with a single type of monomer or with a mixture of two or more different monomers. A polymer which is produced from the polymerisation of two different monomers is referred to as a copolymer. Similarly, a polymer which is created from three different monomers is called a terpolymer.
What is rubber covalent bonding?
Rubber polymers are normally made up of hydrocarbon monomers which contain only hydrogen and carbon atoms. Hydrogen and carbon atoms are bonded together by covalent bonds, where atoms share a pair of electrons. Covalent bonds allow atoms to have a full outer electron shell without changing their net charge. Due to the number of electrons in their outer electron shells, carbon is only stable if it has four covalent bonds. Hydrogen will be stable when it has one covalent bond.
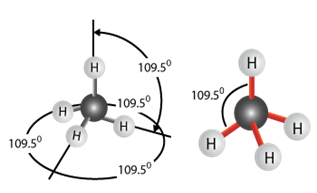
How rubber elasticity works
The four bonds made by carbon are equidistant from each other in three dimensions - they are all 109 degrees apart. This means that the long polymer chains with carbon backbones will not be flat but will have natural angles and kinks in them. When the rubber is stretched, the bond angles will be distorted and the molecules will be “straightened out”. However, as soon as the force is removed the molecules will “bounce” back to their original shape. This is what gives rubber its high elasticity.
What is rubber molecular bonding?
The polymer molecules are bonded together with covalent bonds, these molecules are then attracted to each other by intermolecular bonds. The level of attraction between the molecules depends on how close the molecules are to each other. The closer they are the stronger the attraction will be. Rubber polymers have an amorphous, random shape meaning that they do not fit together perfectly and cannot be stacked tightly on top of each other. This keeps the polymer chains further apart and weakens the intermolecular bonds between them.
What are elastomers?
The weak intermolecular bonds between the polymer chains make rubber behave differently to other engineering materials such as metals or plastics. There's a special quality that makes rubbers “rubbery” and that is its high elasticity. These elastic polymers are known as elastomers. Elastomers are viscoelastic materials, meaning that they exhibit both elastic and viscous behaviours and it takes a high elongation to break or deform. This is due to rubbers high tensile strength.
The weak intermolecular bonds in an elastomer allow the polymer chains to slide over each other. In the raw state, rubbers behave almost as if they were melted and are easily moulded and shaped. However, the weak bonds between the rubber polymer molecules lead to rubbers being less strong than other materials which contain strong bonds between the molecules. Elastomers generally have a low Youngs modulus (measure of stiffness) and high failure strain compared to other materials.
Curing and crosslinks of rubber
In its raw state, rubber has a relatively low strength since it contains weak intermolecular bonds. To make rubber more suitable for industrial uses, the strength of the intermolecular bonds can be increased by crosslinking the polymer molecules.
Crosslinking is when separate polymer chains are bound together by a chemical bond. This process is known as curing or the vulcanisation of rubber, and it produces a rubber with high tensile strength, high elasticity, and a non-sensitivity to a wide change of temperature. The image below shows how polymer chains are held together by the formation of crosslinks.
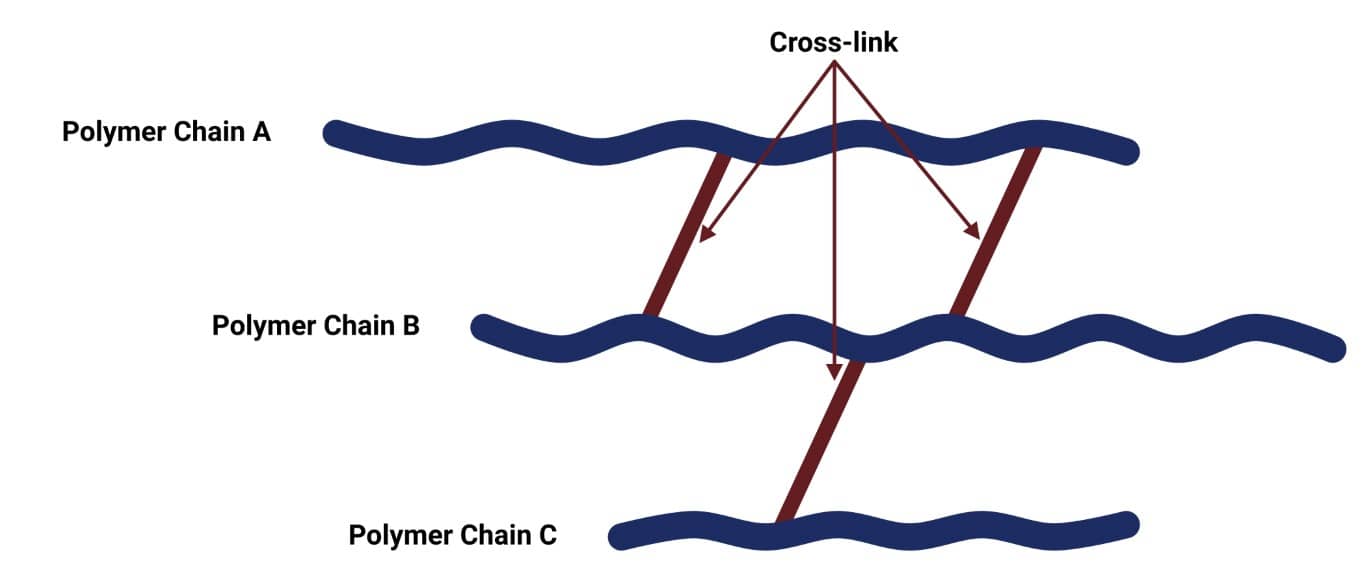
Through crosslinking, the rubber molecules develop a net-like rubber structure reinforcing the material and increasing its stiffness, preventing intermolecular movement of the rubber polymer chains. The more cross-links there are, the less mobility there will be for the polymer molecules. Elastomers are usually lightly crosslinked. This allows the polymers to stretch whilst still retaining their structure.
Prior to vulcanisation, the polymer chains in rubber are held together with weak intermolecular forces. Curing rubber causes the boiling and melting points to increase. The covalent crosslinks formed require a higher amount of energy to break. Rubbers with longer polymer chains also have higher melting points due to the high number of crosslinks between the polymer chains.
Improving the elasticity of rubber
The vulcanisation process increases the elasticity of the rubber. Elastomers are flexible because their long chains have the ability to reconfigure themselves to distribute an applied stress. The covalent cross-links ensure that the elastomer will spring back to its original shape once the stress is removed. The crosslink network formation means, that cured rubber becomes insoluble in any solvent.
The discovery of rubber curing (Vulcanisation)
The process of sulphur vulcanisation was first discovered by Charles Goodyear when he accidentally heated natural rubber and sulphur together. At high temperatures, the carbon-to-carbon double bonds “open up”. This allows the sulphur molecules to react with the carbon atoms to form covalent polysulphide links between the polymer chains. The chemical formula for the reaction between sulphur and a polymer chain is shown in the image below.
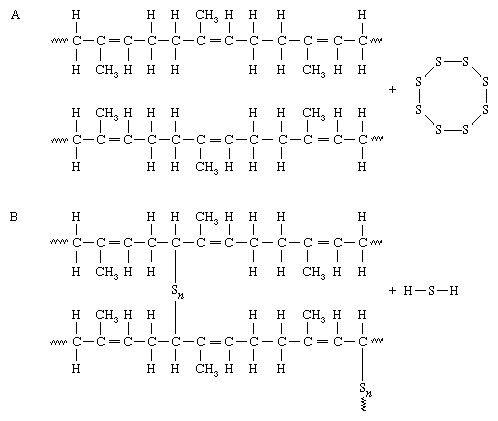
The amount of sulphur added determines how rigid the vulcanised rubber is. A wide range of physical properties of rubber can be obtained by controlling the amount of sulphur and accelerator concentrations in the process of vulcanisation.
Normally about 2 parts by weight of sulphur are used per 100 parts of rubber, this stops the material from becoming too brittle. This method of sulphur curing can only occur when there are double bonds present in the polymer chain. Nowadays, other methods of vulcanisation exist to create crosslinks in different rubbers. To read about this, see our article on Vulcanisation.
Vulcanised rubber will retain its shape and cannot be processed by any means. It can't be mixed, moulded, or extruded again. Vulcanisation must only be performed once the rubber product is in its final geometric form, or you risk wasting valuable rubber.
Can rubber be overcured?
If too many crosslinks are formed between the polymers, the rubber can become over-cured. This results in the hardening of the rubber and loss of flexibility as well as a reduction in tensile strength. On the other hand, under-cured rubber could reduce the strength and compression set resistance, which ultimately affects the quality of the rubber product and could cause it to fail.
Compression set resistance is the measurement of the strain retained in a material once the compression force is removed. It indicates how well the rubber can revert to its original shape.
Determining the optimum cure time
The optimum cure of rubber is the degree of vulcanisation or number of crosslinks which leads to the ideal material properties. The optimum cure time is the amount of time which a rubber requires to be vulcanised to reach this level of cure. This is dependent on the size and thickness of the material as to how long the cure time should be. There's a special instrument that can be used to determine this.
Moving Die Rheometer
A common way to test the cure characteristics of a rubber compound is by using a Moving Die Rheometer (MDR). The MDR can be used to determine the onset of the cure, the cure rate, and the time to optimum cure level. MDR tests are often used to verify that a material meets the desired specifications.
During the test an uncured sample is heated and pressurised inside a sealed test chamber whilst being sheared by the oscillation of the lower die. The heat and pressure cause crosslinks to form between the rubber molecules. As the number of crosslinks increases, the stiffness of the sample will also increase.
This increase in stiffness can be calculated by measuring the torque response of the material. The torque response is related to the resistance of the material to being sheared by the oscillating die. This is proportional to an increase in the low strain modulus of elasticity. The MDR measures the torque of the material using a torque transducer and a graph of torque against time can then be plotted. A typical MDR test graph is shown in the image below.
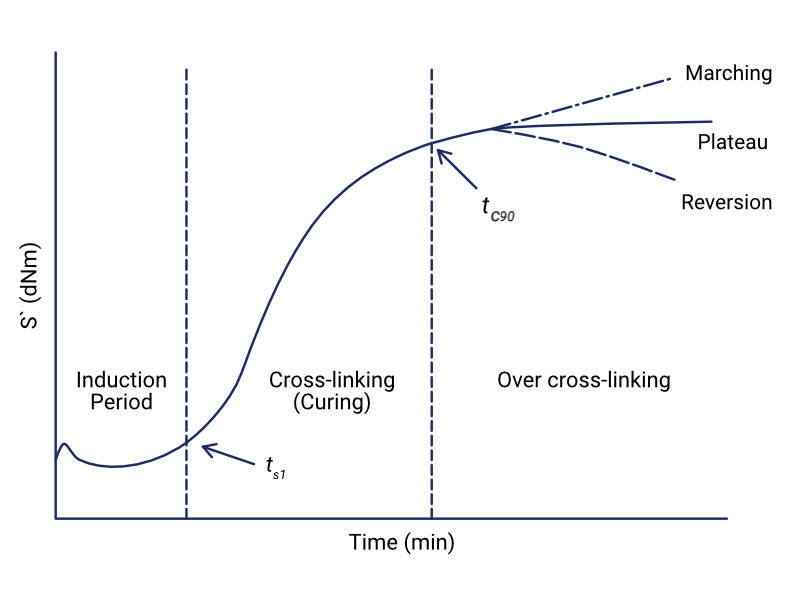
Looking at the curve on the MDR graph, this is an S' curve and shows the cure rate of the material. The cure rate of the material will depend on the temperature at which the test is carried out. This graph depicts the three phases of the curing process: induction period, curing and over curing.
During the induction period, there are no crosslinks between the rubber polymers. The rubber is very fluid at this point and as the rubber material is heated, its torque response decreases until it reaches a minimum value (ML).
As crosslinks begin to form in the rubber, the torque increases. The curing period of the rubber begins at ts1. This is the time at which the torque increases from the minimum value by 1 unit (ML + 1), and it gives an indication as to when crosslinks begin to form in the rubber. The time in which rubber can be heated without vulcanizing is known as the scorch time.
Scorching is the undesired early vulcanisation of rubber during processing and can lead to a decrease in plasticity and mobility, meaning that the material cannot be easily shaped or moulded. The longer the scorching time, the less likely that scorching will occur during processing.
The optimum cure for the rubber occurs at tc90. This is the cure time at which 90% of the cure has taken place. After tc90 time has elapsed, the material will enter the overcure period. Continuing to heat the rubber past the optimum cure can cause marching or reversion. Marching can happen because of a continuous occurrence of crosslinking reactions and can lead to instability of the final cured material.
Conversely, a decrease in torque after the maximum has been reached, indicates a reversion of the crosslinking process in the compound. This reversion is caused by the thermal ageing of the rubber. To read more about this phenomenon, have a look at our article on the Ageing of Rubber Materials.
The results from a Moving Die Rheometer test are helpful in indicating the scorch time and the optimum cure time of the temperature and pressure of the rubber. Other properties of the rubber can be determined from the MDR graph such as the hardness of a cured material which can be estimated from the max value of the cure rate curve.
What are the properties of rubber?
Rubber is a unique material which behaves very differently to other engineering materials such as plastics and metals. It is very “bouncy” and has a high elasticity. This means, if it is stretched it will return to its original shape. Other important properties of rubber are its flexibility, strength, permeability to water (not soluble in water) and high abrasion resistance. Rubbers also tend to have high melting and boiling points.
Due to its mechanical properties, rubber is extremely versatile and can be useful in many applications whether it's automobile tyres or heart valves or gaskets in jet planes. A major advantage rubber has over other engineering materials is its elasticity. Rubber is often used in seals and gaskets due to its ability to deform and revert back, unlike other materials. Seals and O-rings are often made from rubber as it is durable, highly flexible and can be easily moulded to fit any shape. Many synthetic rubbers are oil-resistant which makes them a great choice for oil seals or petrol hoses.
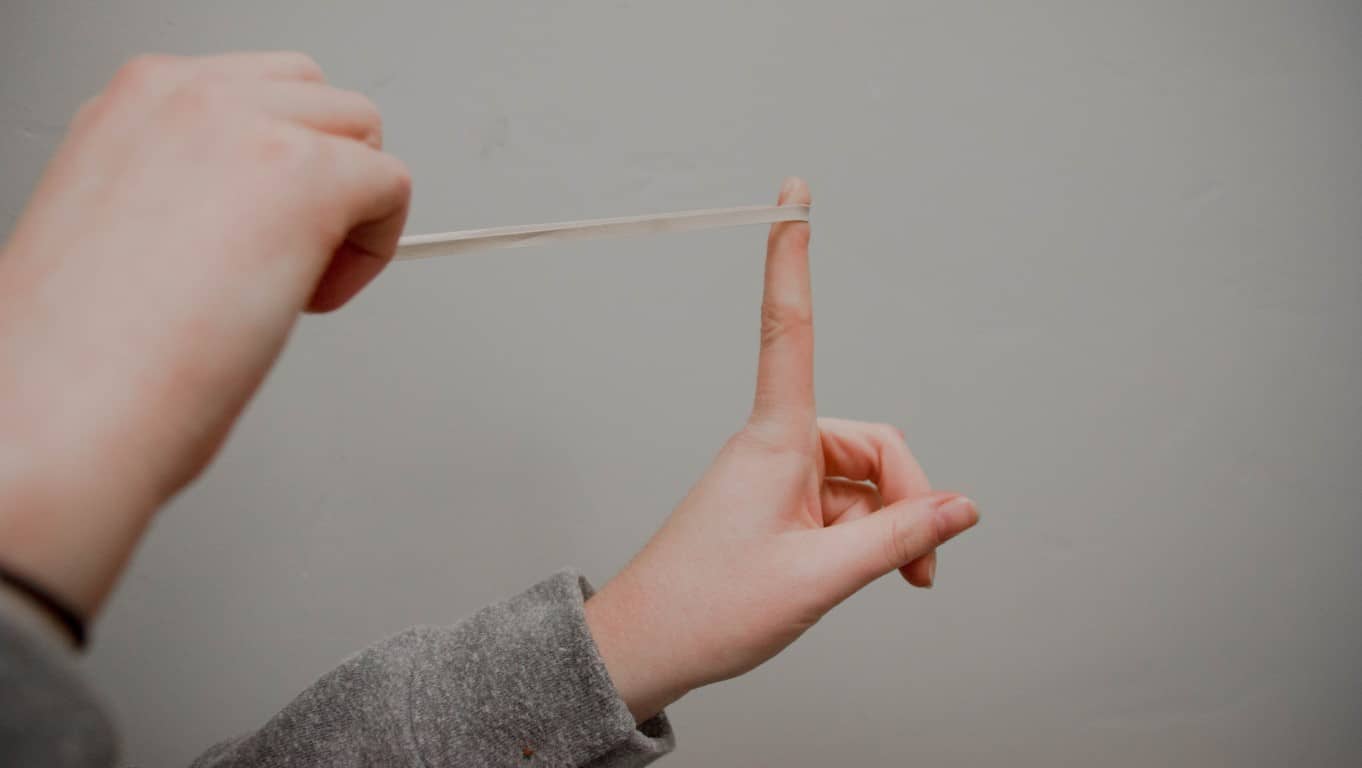
The behaviour of rubber
The behaviour of a material is governed by its chemical structure and the behaviour of its molecules. Normally, elastomers require vulcanisation before they can be used. Unvulcanised rubber has a similar consistency to chewing gum which isn't very strong, does not return to its shape once its structure is compromised and becomes sticky when hot. As rubber warms up, the polymer chains flow over each other. This is a useful property as it allows us to easily shape the rubber. This quality however is usually less desirable in the final rubber product and so the rubber can be cured to change its material properties. Vulcanisation causes crosslinks to form between molecules and stops the flow of chains over each other.
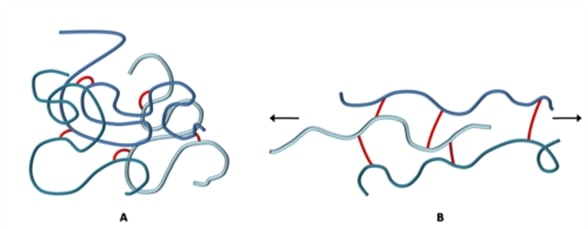
Vulcanised rubber is very elastic. The image above illustrates the behaviour of the crosslinked rubber under tension. The crosslinks prevent the chains from flowing relative to each other and will pull the polymer chains back into their original position once the load is removed. Some rubbers may be stretched up to 10 times their original length and will still return to their original size and shape once the external force is removed. Another very important quality of elastomers is that they have a very low compression set. This means that an elastomer will return to its original dimensions once the force is removed even if it has been under compression for a long period of time.
What are the applications of rubber?
Rubber absorbs energy as it deforms and recovers, making it a great material choice for buffer sections to provide impact protection. It's also commonly used as shock and vibration absorbers such as in car suspension, earthquake bearings, rail pads and bridge bearings. Rubber is also used in springs which allow, relatively high levels of deflection and can hold considerably more weight than other springs. When selecting a rubber for these applications it is important to consider its resilience. Resilience is defined as to how well the material can “spring back” to its original shape after being subjected to a heavy load. Depending on the application the rubber may be required to absorb or give back more energy.
Rubber absorption
In a shock absorber, the rubber is required to absorb the external energy which is acting on it. In this instance, a low resilience rubber should be chosen. Low resilience rubbers exhibit better wear and less heat loss. On the other hand, a rubber with high resilience should be chosen for a spring like application as this will allow the rubber to “bounce” back and give back the energy which is put into it. Most applications require that the rubber exhibit a behaviour which is a balance between a spring and a shock absorber.
Another use for rubber is in shock mats which can be used in gyms, construction sites and industrial workplaces. The rubber mats are used to protect the flooring and equipment by absorbing and dissipating the incoming energy. Rubber will return to its original shape even after being compressed for long periods of time due to its low compression set.
Rubber insulation
Another important feature of rubber is its ability to insulate. Rubber is widely used in electrical mats and wire cables as well as being used for overhead power line spacers. Electricity cannot flow through rubber as the electrons are tightly bound and are not able to move freely. Rubber has a high melting and boiling point meaning that certain rubbers can be used in very high-temperature applications.
Choosing the right rubber to use
When choosing the right properties for a particular application, it is important to remember that the rubber does not always need to exhibit high levels of each material property. The rubber should be chosen based on the intended use of the material. For example, if you're looking for rubber used in the food or pharmaceutical industry then you would choose silicone, as it is non-toxic and FDA-approved.