Extruding Rubber Parts
Extrusion Process
The rubber extrusion process is how rubber companies produce, lengthen and shape customer orders.
What is rubber extrusion?
Rubber extrusion is the process of turning raw rubber materials into varying lengths with constant cross-sections. This is conducted using an extruder which pumps out the rubber materials through a shaped template like a playdough machine.
Soft, un-cured synthetic or natural rubber is loaded into the extruder and forced, under high pressure, through a shaped die. This die forces the rubber into the desired cross-section. Then, the extrusion will typically need to be cured or vulcanised to be rendered usable.
What are the different types of extrusion machine?
In the rubber manufacturing industry, there are two different types of extruding machines: the Screw Extruder and the Ram Extruder. Many different industries use extruding machines: the food industry extrudes pasta; the aerospace and automotive industries extrude metal shafts; the plastic industry extrude plastic tubing; and the rubber industry extrude rubber fendering.
What are the basic components of a rubber extruder?
The extruder machines look different depending on the industry, however, they all operate in essentially the same way. In the simplest form, an extruder consists of four basic components:
- Drive system: Consisting of the motor and power transmission units.
- Barrel: Where the rubber is fed.
- Transporting unit: Typically, a ram or screw.
- Head: Holds the die that ultimately turns the material into the desired shape.
In industry, extruders have been categorised in different ways: by transporting unit, such as screw or ram extruders; or by the temperature of the material fed into the extruder, such as hot or cold feed extruders. But the fundamental distinction between the two types of extruders is in the mode of operation, which are:
- Continuous: Delivers rubber in a continuous manner and has a rotating member or screw; here the pressure is produced by a screw.
- Discontinuous: Delivers rubber in an intermittent fashion and has a reciprocating ram or screw, these types of extruders are ideally suited for batch type processes such as injection moulding.
It is important to note that extruders are usually designated by the diameter of the extruder barrel or the length to diameter (L/D) ratio.
How does a screw extruder work?
In a screw extruder, material is continuously fed into the hopper and heated by the heaters along the barrel until it rises to a temperature that makes it easy to shape. The rotation of the screw forces the material toward and through the die, producing the extrusion of desired length and cross-section. Notice how the shape of the screw gets larger the closer it gets to the die? This compresses and mixes the material, reducing the amount of trapped air and makes the material more homogenous.
There are different variations of screw extruders which are, single, twin and multi-screw extruders. As the names suggest, the difference is the number of screws inside the barrel. Each variation has its place and has different advantages and disadvantages.
The advantages of a single-screw extruder
The benefits from using single-screw extrusion are:
- Very high throughput.
- Capable of handling a wide range of materials.
Single-screw extruders do, however, struggle to mix certain materials like pasta and powder, sometimes rendering them unsuitable.
Twin and multi-screw extruders in comparison have:
- Higher pumping efficiency.
- Better mixing capabilities.
- More uniform and quicker heating of the material.
- Better handling of high moisture and sticky materials.
- Self-cleaning and higher material use efficiency.
However, these types of extruders come with higher costs, both initial and operation costs. They are also more complex, leading to them being less robust than their singe-screw counterpart. Additionally, the single-screw extruder is far superior to twin- and multi-screw extruders at handling materials that are more common.
How does a ram extruder work?
In ram extruders, a quantity of warm compound is placed in the barrel, the die is attached to the head of the barrel and the ram forces the material through the die to form an extruded product.
The advantages of ram extruders
There are many advantages to using ram extruders, these are:
- Extrusions can be carried out at lower temperatures than single-screw extruders.
- Difficult compounds can be extruded.
- Easy to clean.
- Useful for short runs.
- Useful for compounds which need to be strained through gauge for quality products requiring completely contamination free material.
- Almost no material losses, leading to large savings.
The major disadvantage of the ram extruder is that it is not a continuous process, meaning that the volume of rubber that is possible to put into the ram is limited.
Swell and shrinkage during extrusion
Swell (or die swell, extrudate swell and Barus effect) is a common phenomenon in polymer manufacturing. It occurs due to the material attempting to return to its original shape after having been compressed by entrance into the die. Factors that affect the swell of the material are:
- Rheological characteristics of the material.
- Shape of head and extrudate.
- Pressure in the head.
- The head and compound temperatures.
What are the benefits of rubber extrusion process?
The benefits of the rubber extrusion process are
- An efficient and economical manufacturing process.
- The volume of wasted material in this process is minimal.
- A continuous process that can produce finished products of different lengths in a variety of shapes.
What are the benefits of extruded rubber parts?
The benefits of extruded rubber parts are:
- Lightweight, flexible, extremely durable, and long-lasting.
- Highly resistant to chemicals, heat, cold, aging, fatigue, friction, abrasion wear and tear.
- Ideal for use in a myriad of harsh or extreme conditions.
Where are rubber extruded parts used?
Rubber extruded parts have been commonplace for over 100 years now, having been employed in 1000's of different applications during that time. A few examples are given below:
- Door and window seals
- Edge trim profiles
- Bumpers and fenders
Door and Window Seals
Also known as top and side seals, these profiles are designed to fill the gaps between doors and door frames to prevent wind and water from entering a vehicle or building. They are used in cars and trucks, as well as in many commercial and industrial facilities. Door seals such as hatch seals can also be found in fuel tanks, rooftop HVAC systems and in electronic enclosures.
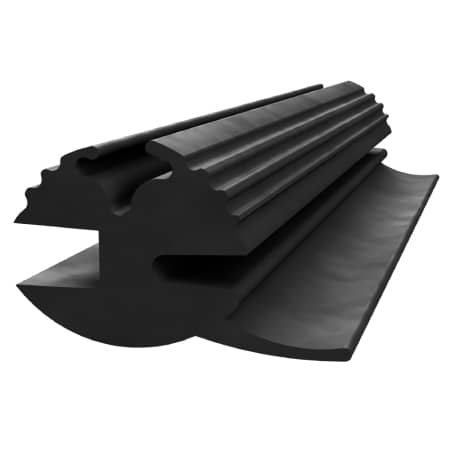
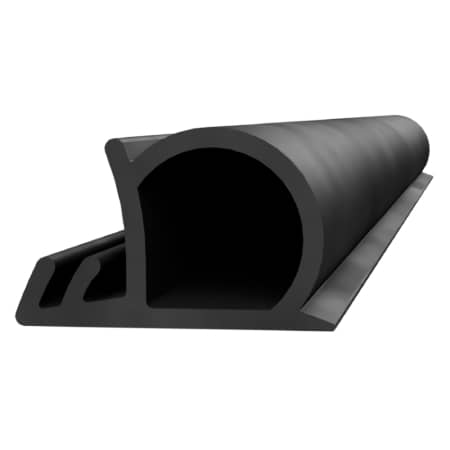
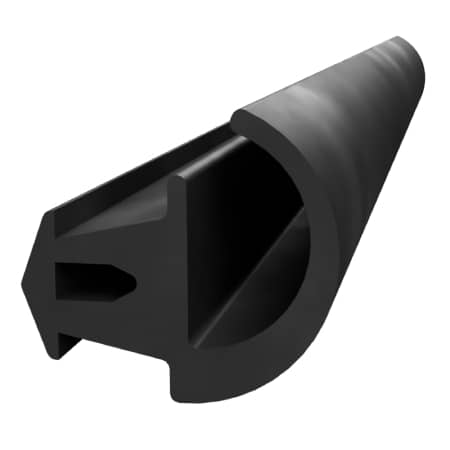
Edge trim profiles
Edge trim profiles are used to cover rough edges made from plastics and steels. These types of rubber extruded profiles are made from flexible materials and have gripping tongues that allow them to provide a much stronger hold. Edge trim profiles are usually found in automotive and marine industries and are used for applications such as decorative trims for boats, cars, and buildings.
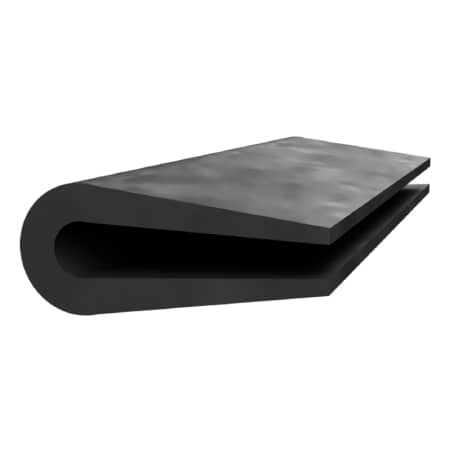
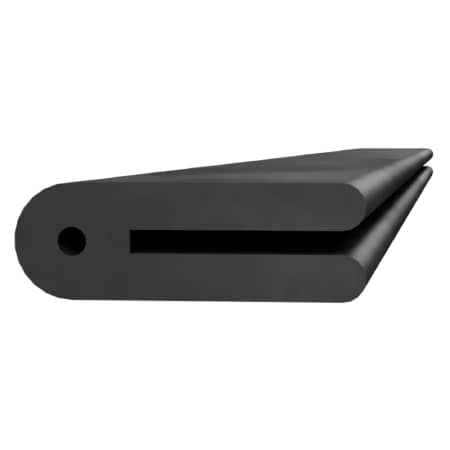
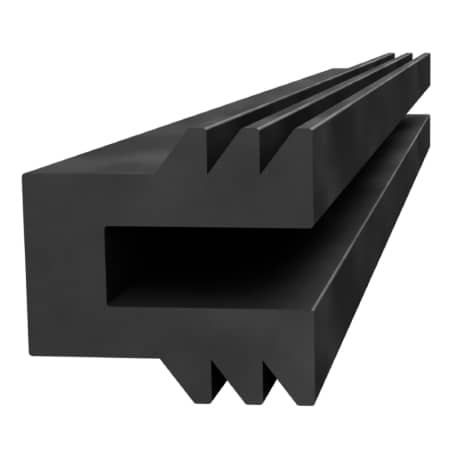
Bumpers and Fenders
Rubber bumpers and fenders protect the hull and berthing infrastructure from damage when vessels berth alongside. The fender functions as a shock absorber by absorbing the energy of a vessel on the berthing facility. There are many service factors which must be taken into consideration when deciding on which type and size of fender is best suited for a given application. D-shaped bumpers are also used on the rear of trucks and trailers to protect the vehicle from damage when reversing into loading docks.
Whether by extrusion or any other rubber processing methods, there is no denying that rubber is an excellent material for many everyday applications.
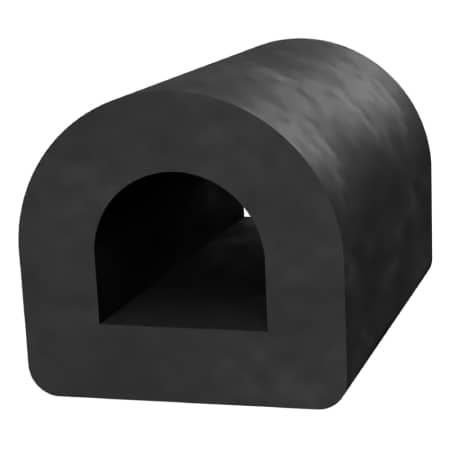
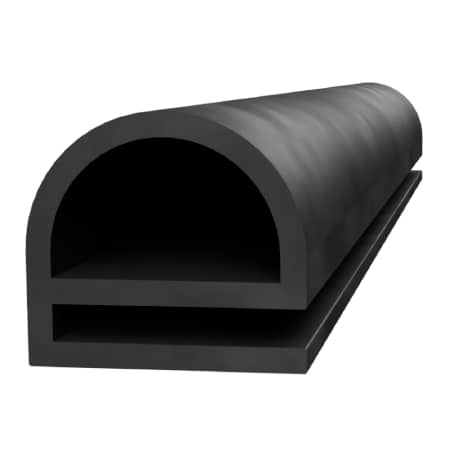
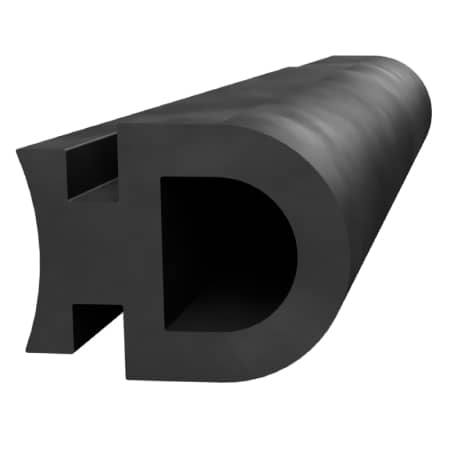
What comes after the extrusion process?
A wide variety of additional processes can be applied to rubber extrusions. Some of these operations may be completed by standard or custom devices added inline to the extruder. Alternatively, post-extrusion processes can be performed offline by people and/or additional equipment at the extrusion facility. Common examples of post-extrusion processes include:
- Punching
- Cutting
- Printing
- Drilling
- Moulded corners
- Riveting
- Grinding
Punching
Extruded products that go on to be bumpers, fenders or hatch seals usually require holes or slots to punched into the rubber. These can be in an assortment of shapes and sizes and could be applied to parts for fasteners, venting and alignment.
Cutting
Not all extrusions are at their required length once vulcanised. The rubber extrusions can now be cut to their specified length, or they can be cut conveniently for shipping purposes. Tighter tolerances can be achieved as well as angles or mitres with an offline cut. Fly cutters and guillotines can be used to cut smoother or shorter lengths of extrusion very quickly.
Printing
After vulcanisation, printing numbers inline offers traceability options. Printing identifiers such as websites, phone numbers, time and date, lot/batch, patent I.D. numbers and in some cases, barcodes can be added to the parts.
Drilling
Drilling is very similar to punching, holes and slots can be drilled into extrusions after vulcanisation. This method is capable of handling thicker and harder materials than the punching process.
Moulding corners
After the extrusion process, it's possible to take two extrusions and mould them together. This enables the creation of frames and corners for applications such as container door seals and window seals.
Riveting
Specific extrusions can be riveted to other materials to produce specialist products, such as the flexible rollaway bank ladder.
Grinding
Extrusions can be grinded to achieve a specific surface finish and to add custom features.