Rubber Gaskets Manufacturer
Delivering custom rubber gaskets in industry-leading delivery times
Make Walker Rubber your first choice to make your rubber gasket design a reality.
Rubber gaskets manufactured to meet your needs in days, not weeks. Offering some of the most competitive lead times in the UK, Walker Rubber have decades of knowledge combined with state-of-the-art equipment and will not be beaten on quality.
Sheet material comes in many different forms including: rubber, sponge, foam, compressed fibre, cork and plastic. With a wide range of over 100 different sheet material combinations in stock and 1000s more to choose from, we are well prepared to turn your drawing into a product in next to no time.
Our digital cutter has a bed over 2m wide, combined with an indexing belt, we can produce some of the largest gaskets on the market. Don’t worry, we can also manufacture rubber gaskets as small as just a few mm across. Our ability to cut rubber gaskets doesn’t just stop at width, we can also cut rubber as thin as 0.25mm all the way up to 50mm thick ensure we have every combination covered to meet your requirements.
At Walker Rubber there is no minimum order, whether you need 1 rubber gasket or 1000 rubber gaskets, we can fulfil your needs. Through investment in the latest cutting equipment, 99/100 times we will be able to produce your gaskets without a tooling charge, cutting straight from your 2D CAD file.
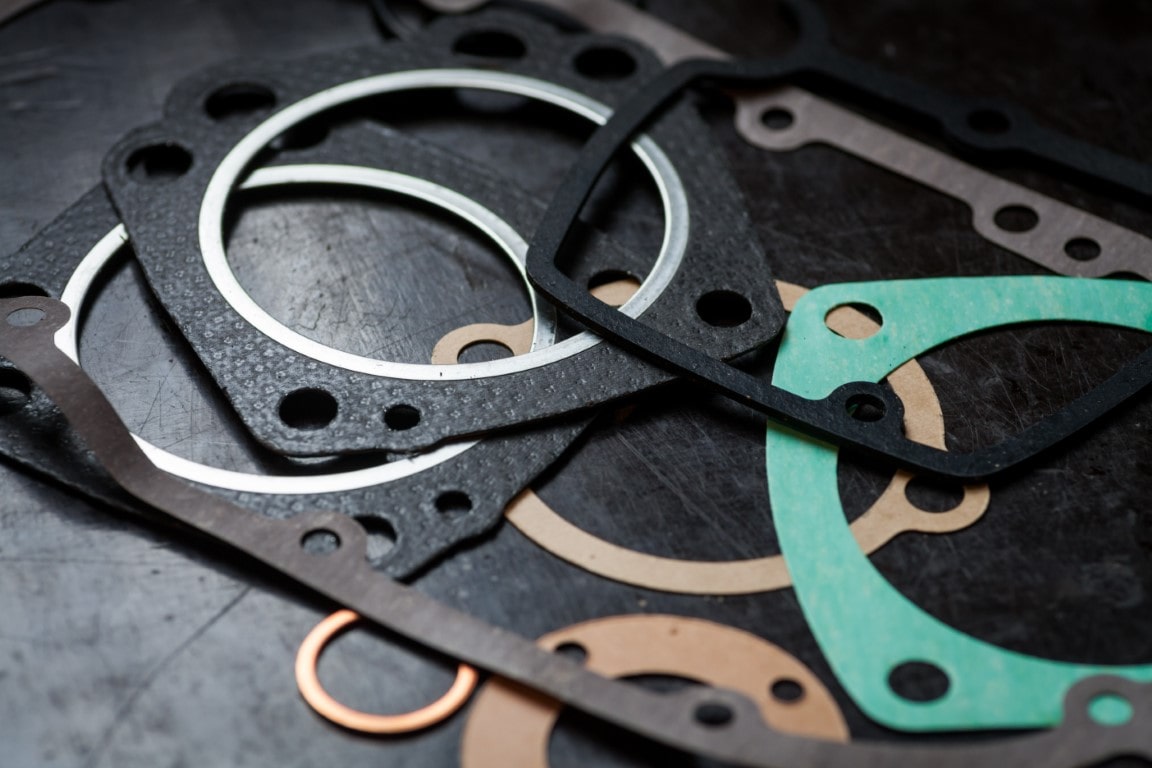
Rubber gaskets your way
At Walker Rubber we manufacture our gaskets to your needs. We can provide your rubber gaskets, washers and seals in a wide range of forms, from thin to thick, round to square. We offer a range of grades, including:
Rubber gaskets your way
At Walker Rubber we manufacture our gaskets to your needs. We can provide your rubber gaskets, washers and seals in a wide range of forms, from thin to thick, round to square. We offer a range of grades, including:
The Walker Rubber Difference

Delivery
Made to order rubber gaskets in industry leading turnaround times; Order to delivery in just 3 working days but typically next day.

Support
Not quite sure what you need? Our team are on hand to provide fast, high-quality expertise with years of experience to back it up.

Service
Our sales team will guide you through the process every step of the way. We are proud to say 90% of enquiries are quoted on the same day ensuring there is no delay.

Quality
With our right first-time ethos, combined with only using premium materials from trusted sources, the quality of our rubber gaskets are the best in the business.
Learn More About Rubber Gaskets
Our knowledge hub is packed with information to help you in your next project! Visit the page below to get a more in-depth look at rubber gaskets.
Cutting rubber Rubber engineering tolerances